Developing resilient plasma-facing materials (PFMs) to enable fusion power
Fusion Energy is a sustainable clean energy source that does not produce greenhouse gases. Nuclear fusion is the process that powers the stars, in which very light elements fuse together to create heavier elements, releasing energy. The race to introduce commercial fusion power is well underway to meet humanity’s growing energy needs without producing greenhouse gases and both drastically increasing safety and reducing radioactive waste compared to current nuclear technologies. We are committed to establishing a fusion materials supply chain built from the ground up to serve the needs of the emerging nuclear fusion power industry.

Inside a reactor, such as the donut-shaped tokamak shown here, the fusion process occurs within a super-hot plasma contained by very strong magnetic fields. The walls of the reactor, however, are subject to extremely high temperatures and intense radiation loads that would destroy most materials. In order to continuously operate a reactor, advanced materials are needed that maintain good mechanical properties at 1000°C or higher, can survive very fast changes in temperature, and are resistant to radiation damage. We are developing a multifaceted tungsten-based plasma-facing material (PFM) solution to survive this extreme environment. Advanced bulk manufacturing approaches are used to improve the typically brittle nature of tungsten, allowing us to take advantage of its extreme temperature tolerance and develop robust and reliable components for fusion, such as the wall tiles shown here, advanced drill bits, hypersonic cooling systems, and more.
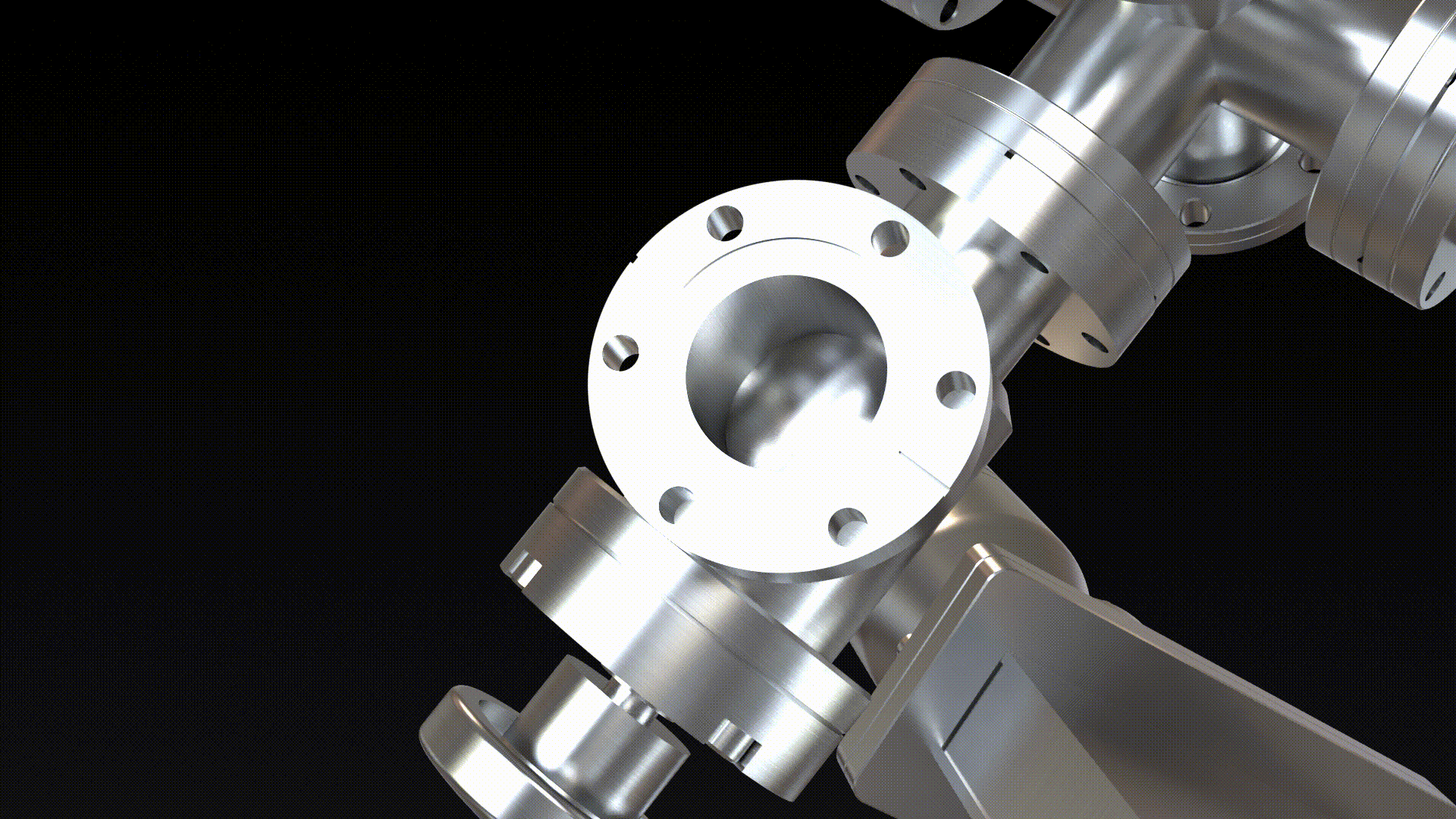
Directed Irradiation Synthesis (DIS)
Is a unique approach to nanotechnology, capable of transforming the existing surface of nearly any material into new nanoscale textures and morphologies that change the way it interacts with its environment. Within fusion we are developing a surface treatment for tungsten to help it support a liquid metal surface, such as lithium, to provide an additional layer of wall protection. Other applications include solid-liquid interfaces in thermal transport systems and even the surface of medical devices within the body.
DIS has the power to reorganize matter on a surface into new surface textures and morphologies smaller than 100 nanometers. Manipulating atoms on this scale has the power to change the way a device interacts with its environment, enhancing surface properties or introducing new ones while leaving bulk properties, like strength, intact. DIS is significantly faster and cheaper than competing methods, is energy efficient, and neither uses nor produces toxic chemicals.
The DIS process bombards a surface with a proprietary mixture of energetic particles, inducing the controlled self-assembly of atoms into different configurations. The animation demonstrates a component being modified with the purple particle beam within our facility. The size and shape of the new nanoscale features are controlled by adjusting key parameters, allowing the final surface properties to be tuned to match their desired functionality.
Explore the Applications
Discover how our innovative products can transform your business.